Tecnología
aplicada
Proyectos I+D+i
en aquaclean®
Investigación, Desarrollo e Innovación
Para aquaclean group, la innovación y el desarrollo forman parte importante del crecimiento continuo de la empresa, adoptando las últimas tecnologías en el sector para hacer frente a un mercado cada vez más exigente y competitivo. Gracias a la fuerte inversión que aquaclean group realiza en este campo, la empresa ha desarrollado aquaclean technology, una revolucionaria tecnología especializada en tejidos para el tapizado de sofás que simplemente con agua y en tres fáciles pasos elimina todo tipo de manchas de nuestros tejidos.
Gracias al esfuerzo y a la inversión en I+D+i, aquaclean group ha desarrollado una serie de tecnologías y avances en el sector textil que marcan claramente la diferencia con la competencia.
Nuestros Proyectos
Tecnología aquaclean®
Tecnología Safe Front
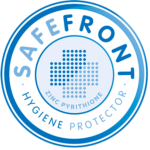
Tecnología Stain Free
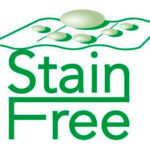
FEDER IDI-20150291
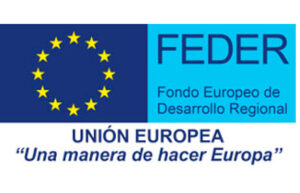
Proyecto de ahorro y eficiencia energética en la industria
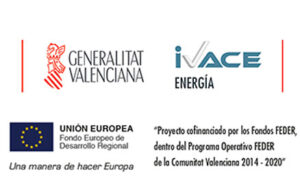
Proyecto mejora energética de la iluminación de la empresa
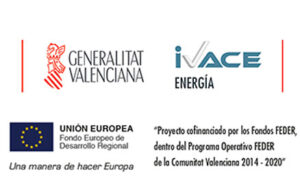
Fondos FEDER AYUDAS ICEX / FERIA MOOD 2017
Antecuir
Antecuir ha participado en la Feria del sector Textil-Hogar MOOD 2017 celebrada en Bruselas, y ha contado con el apoyo de ICEX, así como con la cofinanciación de fondos europeos FEDER, habiendo contribuido según la medida de los mismos, al crecimiento económico de esta empresa, su región y de España en su conjunto.
Interfabrics
Interfabrics ha participado en la Feria del sector Textil-Hogar MOOD 2017 celebrada en Bruselas, y ha contado con el apoyo de ICEX, así como con la cofinanciación de fondos europeos FEDER, habiendo contribuido según la medida de los mismos, al crecimiento económico de esta empresa, su región y de España en su conjunto.
Proyecto CDTI LÍNEA DIRECTA DE INNOVACIÓN
Incorporación de nueva tecnología con los últimos avances de Texturizado en la empresa
La incorporación de una nueva máquina texturizadora por aire de alto rendimiento ha sido un proyecto CDTI. En este proyecto de innovación que comenzó en agosto de 2016 y que finalizó en octubre de 2017, se ha adquirido una texturizadora que nos permite otorgar volumen y opacidad, entre otras propiedades, a los hilados procesados en INTERFABRICS, con el fin de multiplicar las posibilidades de procesado de los hilos (colores, grosor, nudos, opacidad, etc.). Gracias a la adquisición de esta nueva máquina hemos ampliado nuestros servicios internos, con lo cual ya podemos desarrollar y fabricar internamente hilados de alta calidad y con nuevas innovaciones, ya que carecíamos de un proceso de hilatura interno, con lo cual obtenemos múltiples opciones, posibilidades y efectos en cuanto a: combinación de colores, variación del grosor, diferente número de nudos, etc. ofreciendo en los tejidos finales los estándares de calidad que nuestra empresa exige a los artículos.
La nueva máquina que se ha adquirido permite desarrollar internamente nuevos desarrollos de I+D. La empresa con este proyecto se ha diferenciado de la competencia, puesto que este tipo de máquina es totalmente innovadora ya que a fecha actual no hay ningún competidor nacional que disponga de ella en sus instalaciones. La implantación de la nueva máquina ha sido estratégicamente importante para el futuro de la empresa, ya que nos permitirá continuar posicionándonos en el mercado y ser una empresa puntera en nuestro ámbito de actuación.
El resultado ha sido un éxito, ya que la empresa ha innovado y ampliado su tecnología y procesos, pasando a disponer de un nuevo proceso, sin tener que recurrir externamente a la compra de hilados innovadores, para obtener tejidos de alto valor.
LEARNINGTEX
La falta de experiencia en el lugar de trabajo y las habilidades y competencias es uno de los factores que contribuyen a la brecha de habilidades en la Unión Europea en la actualidad. Mientras que 5.6 millones de jóvenes en la UE sufren las consecuencias del desempleo, 36% de las empresas reconocen que es difícil encontrar candidatos con las habilidades que necesitan. Algo está claramente equivocado. La necesidad de identificar, adaptar y adoptar prácticas que puedan hacer frente a este déficit de destrezas es urgente. Esta carencia es muy notoria en el sector textil donde las empresas requieren más personal técnico con habilidades y conocimientos actualizados, que les permita utilizar y manipular máquinas y equipos de alta tecnología para los procesos de fabricación de textiles.
Con este desajuste en el mercado de trabajo cinco instituciones de Austria (BEST), España (AITEX, ANTECUIR y UPV) y Portugal (CITEVE) han puesto en marcha el Proyecto LEARNINGTEX. Tras una evaluación del sector textil en los diferentes paises del consorcio y el análisis de los resultados, las empresas identificaron dos aspectos débiles: los tejidos y los nuevos procesos de control de calidad. Las empresas textiles europeas sólo pueden competir en el mercado mundial por productos de calidad y generar productos de valor añadido. Competir en precios frente a terceros países resulta imposible. La única manera es competir con calidad y en diseño contra el bajo costo y los productos de baja calidad manufacturados en países emergentes fuera de Europa.
El proyecto LEARNINGTEX financiado por el programa Erasmus+ de la Comisión Europea, está en su segundo y último año. El proyecto en el que participa ANTECUIR pretende desarrollar un MOOC (Massive Open Online Course) basado en OERs (Open Educational Resources) sobre tecnologías avanzadas para el control de calidad de los tejidos, no sólo para los empleados obsoletos en materia textil, sino también para los trabajadores inexpertos que acaban de terminar sus estudios. El curso está orientado a los empleados textiles y estudiantes interesados en el conocimiento sobre tejidos, maquinaria y la aplicación de nuevas tecnologías para mejorar los procesos de controles de calidad y reducir los costos.
Actualmente se están desarrollando los diferentes contenidos educativos para el MOOC que serán validados próximamente por ANTECUIR y el resto de socios.
Proyecto CDTI LÍNEA DIRECTA DE INNOVACIÓN
Incorporación de nuevo rame para la implantación de una nueva línea de acabados innovadores
La incorporación de un nuevo Rame y sus equipos auxiliares ha sido un proyecto CDTI Este proyecto de innovación que comenzó en febrero de 2017 y que finalizó en marzo de 2018, ha consistido en la implantación de un rame y sus equipos auxiliares para poder aplicar nuevas propiedades e innovaciones a los tejidos y dotarlos de la máxima calidad con el fin último de convertirse en una empresa vertical que no dependa de los procesos externos del grupo, lo cual está favoreciendo la competitividad de la empresa, en cuanto a una mejora del servicio y una mejora de la calidad final, al poder controlar los acabados a aplicar.
Gracias a esta inversión en el nuevo equipamiento y proceso hasta ahora inexistente en la empresa, experimentará un gran avance técnico y comercial, puesto que INTERFABRICS ya no tiene que recurrir al resto de empresas del grupo, sino que es capaz de innovar los acabados y que estos sean de alta calidad, controlando cada una de las variables. Una de las motivaciones que ha propiciado la nueva inversión, ha sido la diversificación de sus productos hacia nuevos tejidos con acabados más innovadores, lo cual a su vez está favoreciendo la cadena de valor del sector textil. La implantación de la nueva máquina ha sido estratégicamente importante para el futuro de la empresa, ya que nos permitirá continuar posicionándonos en el mercado y ser una empresa puntera en nuestro ámbito de actuación.
El resultado ha sido un éxito, ya que la empresa ha innovado y ampliado su tecnología y procesos, pasando a disponer de un nuevo proceso, sin tener que recurrir a empresas del grupo, para obtener tejidos de alto valor añadido.
LEARNINGTEX
ANTECUIR participa en el proyecto LEARNINGTEX cuyo MOOC será presentado en octubre como un curso online abierto sobre control de calidad textil. Después de completar la creación de los contenidos digitales, el proyecto LEARNINGTEX está centrando sus esfuerzos en la validación y finalización de los OER (Open Educational Resources) que darán forma al MOOC (Massive Open Online Course) sobre control de calidad textil mediante el uso de tecnologías avanzadas.
En los últimos meses los OERs han sido presentados a diferentes audiencias y grupos objetivos en los diferentes países que componen el consorcio. Los participantes han tenido la oportunidad de colaborar en el proyecto evaluando la adquisición de conocimientos en el área por medio de la visualización de primera mano de los recursos creados.
Durante los meses de julio y agosto, los OER han sido finalizados y se alojarán en la plataforma para MOOCs con el fin de ser presentados al público en septiembre y octubre y estar disponible para las partes interesantes.
La primera presentación tendrá lugar en Alcoy en el Campus de la Universitat Politècnica de València, seguida de otras presentaciones en los demás países del consorcio.
El presente proyecto ha sido financiado con el apoyo de la Comisión Europea. Esta publicación (comunicación) es responsabilidad exclusiva de su autor. La Comisión no es responsable del uso que pueda hacerse de la información aquí difundida.
COLOMBIATEX 2019
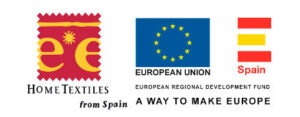
Tecnología aplicada al sector textil con innovación
Proyecto de investigación de una nueva tecnología de producción de hilo símil-chenilla a partir de fibras de origen reciclado de rpet
CONSOLIDACIÓN DE LA CADENA DE VALOR EMPRESARIAL
La empresa INTERFABRICS, S.L., está llevando a cabo un proyecto que cuenta con la ayuda de la Agencia Valenciana de la Innovación (AVI) dentro de la actuación “Consolidación de la cadena de valor empresarial”.
El proyecto CHENITEX NON PLASTICS tiene como objetivo la investigación de un proceso tecnológico alternativo con el que desarrollar un novedoso hilo símil-chenilla a partir de material reciclado. Esta innovadora propuesta en cuanto al proceso y al material además debe permitir solucionar uno de los problemas principales que presenta el hilo de chenilla tradicional, que es la emisión de microfibras durante su fabricación, manipulación y tejido, así como durante toda su vida útil.
A lo largo de las fases de este proyecto, mediante el desarrollo del proceso se pretende crear y optimizar un nuevo tipo de hilo más sostenible debido al uso de materiales reciclados y que puede contribuir a minimizar el impacto medioambiental evitando que los restos emitidos se acumulen en las aguas residuales de las industrias textiles y presenten un problema de contaminación en nuestras aguas y en el ecosistema en general.
Para conseguir el objetivo perseguido, se ha diseñado un plan de trabajo en el que en primer lugar, se estudiará la utilización de un filamento sustitutivo de origen reciclado como puede ser el hilo de poliéster reciclado (rPET) y se analizarán los requisitos funcionales que debe cumplir.
A continuación, se pretende realizar una investigación de las tecnologías de procesado de hilo para explorar nuevas vías de desarrollo mediante los recursos que cuenta AITEX y que proporcionen al material las características y el acabado esperado, y constituyan un avance al estado actual de la técnica. Para ello, se partirá del texturizado por jet de aire ATY (Taslan®) y se enlazará con el proceso de hilatura por huso hueco (hollow spindle) para obtener hilos con efecto chenilla que no presenten problemas de emisiones al medio.
De esta manera se impulsa el modelo de economía circular dentro del sector textil autonómico y se implementa el uso de materiales más sostenibles y reciclables, dando como resultado productos de un alto valor añadido y causando un impacto favorable en la cadena de valor.
INTERFABRICS S.L.
Actuación: Consolidación de la cadena de valor empresarial
Proyecto: Investigación de una nueva tecnología de producción de Hilo símil-chenilla a partir de fibras de origen reciclado
Expediente: INNCAD/2022/165
Subvención: 51.697,10€
Neo-Recycling
El proyecto NEO-RECYCLING, financiado por el Centro para el Desarrollo Tecnológico Industrial (CDTI) y que ha completado su primer hito en agosto 2023, tiene como objetivo principal investigar y desarrollar productos y tecnologías de bajo impacto medioambiental con aplicación en el proceso de fabricación de bienes de consumo tales como nuevos hilados para indumentaria/textil-hogar, textiles de tapicería, calzado, colchones/toppers, composites, compuestos de caucho/elastómeros y piezas de material plástico, basados en nuevos modelos de economía circular.
Para este fin, el proyecto está contemplando los siguientes objetivos técnicos generales y líneas de trabajo principales:
• Investigar y desarrollar nuevos materiales derivados de fuentes renovables.
• Reducir el impacto medioambiental mediante nuevos procesos productivos, haciendo del ecodiseño el eje central sobre el que pivotan estos.
• Desarrollar y validar tecnologías de procesado más respetuosas con el medio ambiente, con una reducida huella de carbono y huella hídrica.
• Estudiar procesos de revalorización de residuos de procedencia diversa (pre- y post-consumo), que generen materia prima reciclada con la calidad suficiente para ser incorporada en procesos productivos a nivel intra- e intersectorial, promoviendo así el concepto de economía circular.
• Actualizar conocimiento respecto de diversa normativa aplicable al respecto, tanto en lo que se refiere a gestión de residuos como a su revalorización y uso.
• Desarrollar nuevos prototipos de productos, proceder a su caracterización de prestaciones y validarlos a nivel técnico-económico.Implementar herramientas de evaluación objetiva del carácter sostenible de la solución obtenida, principalmente a través de ACV, a fin de que las empresas participantes en el proyecto amplíen su conocimiento en técnicas como la indicada y en procesos de ecodiseño, para poder ofrecer a sus clientes bienes, procesos y servicios con soluciones sostenibles reales y con una reducción cuantificable del impacto medioambiental.
Derivado de los resultados del proyecto, de forma cuantitativa se pretende alcanzar incrementos del 15-20% en aspectos tales como la cantidad de material renovable/reciclado de un producto/envase concreto, y reducciones del 15-20% en peso de materia prima utilizada, en el agua empleada en la fabricación, en lacarga contaminante de dicha agua, en el peso de residuo generado o en los kg de CO2 eq. emitidos por un proceso concreto.
El proyecto tiene una duración prevista de 42 meses, desde marzo del 2022 hasta agosto del 2025, estando dividido en 3 hitos de ejecución. El consorcio NEO-RECYCLING, liderado por INTERFABRICS S.L., lo componen siete empresas de sectores manufactureros tales como el textil (HILATURAS FERRE S.A., CREACIONES JEAN PAUL S.L. y la propia líder del proyecto), el calzado (THE ART COMPANY B&S S.A.), el sector descanso (ECUS SLEEP S.L.), el sector plástico (PLÁSTICOS ERUM S.L.) y de la industria del caucho (MCE MEZCLAS CAUCHO S.A.). Adicionalmente, en esta iniciativa toman parte tres Organismos de Investigación: la Asociación de Investigación de la Industria Textil (AITEX), la Universidad Miguel Hernández de Elche (UHM) y la Universidad Politécnica de Valencia (UPV).
NEO-RECYCLING cuenta con un presupuesto de casi 5,39M € y una aportación de CDTI de algo más de 4,58M €.
Plan de Recuperación, Transformación y Resiliencia
Proyecto acogido al programa de incentivos ligados al autoconsumo y almacenamiento, con fuentes de energía renovable, así como a la implantación de sistemas térmicos renovables en el sector residencial en el marco del Plan de Recuperación, Transformación y Resiliencia, financiado por la Unión Europea – NextGenerationEU#PlanDeRecuperación
Beneficiario: TEXTILES PASCUAL S.A.
Componente (C7:l1): DESPLIEGUE INTEGRACIÓN ENERGÍA RENOVABLE
Inversión total: 162.094,90€
Importe de la ayuda: 40.523,72€
Potencia (KW): 235
Real Decreto 477/2021
Antecuir
Proyecto acogido al programa de incentivos ligados al autoconsumo y almacenamiento, con fuentes de energía renovable, así como a la implantación de sistemas térmicos renovables en el sector residencial en el marco del Plan de Recuperación, Transformación y Resiliencia, financiado por la Unión Europea – NextGenerationEU#PlanDeRecuperación
Beneficiario: ANTECUIR S.L.
Componente (C7:l1): DESPLIEGUE INTEGRACIÓN ENERGÍA RENOVABLE
Inversión total: 248.802,62€
Importe de la ayuda: 62.200,65€
Potencia (KW): 418
Real Decreto 477/2021
Consolidación de la cadena de valor empresarial
La empresa INTERFABRICS, S.L. ha llevado a cabo recientemente un proyecto que ha contado con la ayuda de la Agencia Valenciana de la Innovación (AVI) dentro de la actuación “Consolidación de la cadena de valor empresarial” y con la colaboración de AITEX como socio tecnológico encargado de aportar conocimiento, difusión y relevancia científico-tecnológica a los resultados obtenidos.
En dicho proyecto, llamado CHENITEX NON PLASTICS, se han desarrollado novedosos hilos y tejidos símil-chenilla (con aspecto y tacto similares a los productos chenilla convencionales, pero con menor emisión de microfibras) a partir de material reciclado y con propiedades mecánicas competitivas. El valor añadido de los productos desarrollados en este proyecto reside en su carácter sostenible. En los últimos años, la importancia del concepto “sostenibilidad” está incrementando de forma exponencial debido a las exigencias gubernamentales en lo relativo a la reducción del impacto medioambiental y al creciente interés por parte del consumidor a la hora de adquirir productos sostenibles. Por una parte, los productos símil-chenilla minimizan la emisión de microfibras durante sus procesos productivos y durante toda su vida útil, lo que supone un menor impacto medioambiental debido a la reducción de la emisión de residuos sobre las aguas residuales de las industrias textiles y durante el lavado de prendas por parte del consumidor. Por otra parte, el uso de poliéster reciclado como materia prima supone una reducción del consumo de materias primas no-renovables y mejora la huella de carbono del producto final.
Como resultado del proyecto, se han desarrollado los siguiente productos: hilos multifilamento de poliéster reciclado con distintas características y valores de tenacidad mejorados con respecto a los existentes en el mercado (pasando de 2,5 g/den a 3,5 g/den de tenacidad); hilos texturizados (ATY) símil-chenilla de poliéster reciclado con distintas características y composiciones; hilos de huso hueco símil-chenilla de poliéster reciclado con distintas características y composiciones (algunos de ellos se han vaporizado para mejorar su tacto e incrementar su volumen); hilos torcidos símil-chenilla de poliéster reciclado con distintas características y composiciones (ATY y Huso Hueco); tejidos símil-chenilla de poliéster reciclado con distintas características y composiciones capaces de sustituir en tacto y regularidad a los tejidos chenilla existentes en el mercado (para asegurar el buen acabado de las muestras, se les ha aplicado un proceso de acabado de “RAME” con aplicación de “AQUACLEAN”). Finalmente, se ha llevado a cabo una validación de los procesos y productos que componen el proyecto a distintos niveles para cuantificar el grado de consecución de los objetivos planteados inicialmente, concluyendo que la emisión de microfibras se ha visto reducida, principalmente, durante los procesos de fabricación y acabado de los novedosos productos símil-chenilla de poliéster reciclado desarrollados.
Por todo ello, este proyecto fomenta la implementación de materiales más sostenibles, principalmente en el subsector Textil-Hogar, ofreciendo como resultado productos de alto valor añadido que impactarán favorablemente en la cadena de valor textil de la Comunitat Valenciana.
Empresa: INTERFARICS, S.L.
Título Proyecto: INVESTIGACIÓN DE UNA NUEVA TECNOLOGÍA DE PRODUCCIÓN DE HILO SÍMIL-CHENILLA A PARTIR DE FIBRAS DE ORIGEN RECICLADO DE RPET
Nº Expediente: INNCAD/2022/165
Subvención: 51.697,10 €